Maintenance in Field Service
Maintenance is a cornerstone of field service operations, ensuring that equipment functions optimally and downtime is minimized. Traditionally, field service organizations were reactive, focusing on fixing equipment after it broke down. However, modern practices emphasize a proactive and predictive approach, which not only improves customer satisfaction but also reduces operational costs. Let’s explore the various types of maintenance activities in field services and their benefits.
Why Maintenance Matters in Field Services
Effective maintenance strategies are essential for ensuring customer satisfaction and operational excellence. Here’s why:
- Cost Savings: Proactive and preventive maintenance reduce the likelihood of costly emergency repairs and production losses.
- Increased Equipment Lifespan: Regular upkeep ensures machines operate efficiently for longer periods.
- Enhanced Safety: Properly maintained equipment reduces the risk of accidents or malfunctions.
- Improved Customer Trust: Reliable equipment performance builds customer confidence and loyalty.
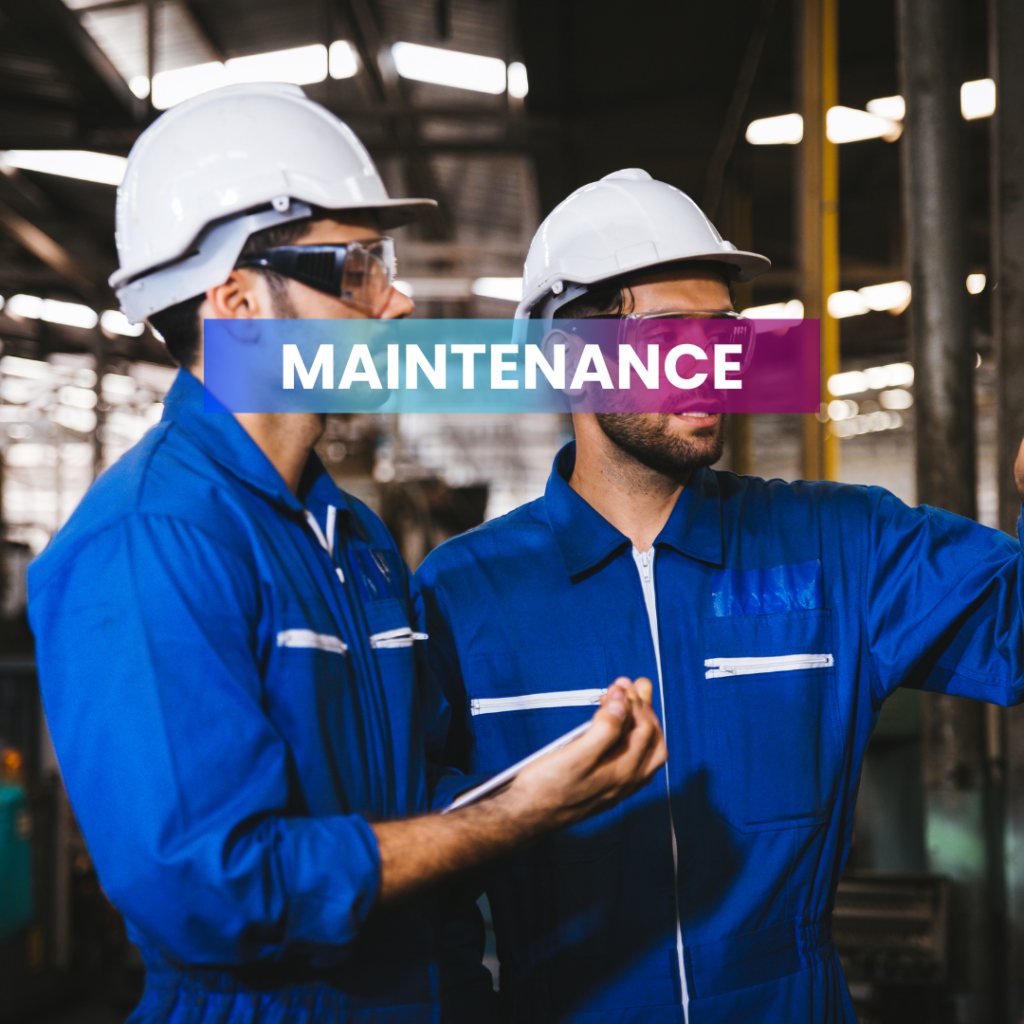
Integrating Maintenance Practices with Modern Tools
Today’s field service organizations leverage cutting-edge technology to enhance their maintenance capabilities:
- Mobile Apps: Allow technicians to access maintenance schedules, record findings, and order spare parts on-site.
- Cloud-Based Platforms: Centralized systems that track equipment history, schedule maintenance, and provide remote support.
- Augmented Reality (AR): Assists technicians with step-by-step guidance during complex repairs or inspections.
1. Corrective Maintenance
Corrective maintenance involves addressing issues after they occur, typically triggered by a malfunction or performance irregularity.
Key Activities in Corrective Maintenance:
- Repairs: Fixing damaged or non-operational equipment to restore functionality.
- Calibration: Ensuring machinery is functioning according to specifications, particularly for precision-dependent equipment like sensors or medical devices.
Advantages:
- Direct response to existing issues.
- Allows for immediate problem resolution, reducing prolonged downtime.
Challenges:
- Can be costly if the breakdown leads to production delays.
- Unplanned repairs may disrupt business operations.
2. Preventive Maintenance
Preventive maintenance focuses on regular, planned activities to inspect and maintain equipment before issues arise.
Key Activities in Preventive Maintenance:
- Routine Inspections: Checking equipment for wear and tear or potential issues.
- Parts Replacement: Proactively replacing components like filters, belts, or gaskets that show signs of wear.
- Lubrication and Cleaning: Ensuring machinery runs smoothly and without blockages.
Technological Enhancements:
- Connected Devices: Using IoT-enabled devices to collect and analyze performance data, providing insights into equipment health.
- Performance Monitoring: Observing real-time data to detect any deviations from normal operation.
Advantages:
- Significantly reduces the likelihood of breakdowns.
- Enhances equipment lifespan and reliability.
- Minimizes unexpected downtime, keeping operations smooth.
3. Proactive Maintenance
Proactive maintenance takes preventive strategies a step further by using advanced tools and analytics to predict potential failures before they occur.
Key Activities in Proactive Maintenance:
- Predictive Analytics: Analyzing historical and real-time data to identify patterns that may indicate future issues.
- Condition-Based Monitoring: Using sensors to continuously assess equipment conditions, such as vibration levels, temperature, and pressure.
- Fault Prediction: Employing machine learning algorithms to compare current operations with optimal benchmarks and flag anomalies.
Advantages:
- Nearly eliminates unexpected breakdowns.
- Reduces the cost of emergency repairs and service disruptions.
- Optimizes the use of spare parts and technician time.
Technological Tools:
- Digital Twins: Virtual models of physical assets used to simulate and predict maintenance needs.
- AI-Powered Systems: Automated tools that identify trends and recommend actionable insights.
Maintenance in field service has evolved from a reactive, “fix-it-when-it-breaks” approach to a proactive, technology-driven strategy. By embracing corrective, preventive, and proactive maintenance practices, businesses can maximize efficiency, minimize costs, and deliver superior customer experiences. Investing in advanced tools and methods ensures that your field service operations remain ahead of the curve, ready to tackle modern challenges with confidence.