Installation in Field Service
Installation is the foundation of effective field service operations. It sets the stage for the long-term functionality and performance of equipment, ensuring that customers experience optimal results from day one. In the context of field services, installation encompasses a range of critical steps designed to seamlessly integrate new equipment into a customer’s operating environment while adhering to industry best practices and specific client requirements.
Benefits of Professional Field Service Installation
- Minimized Downtime: Expert installation ensures quick deployment, reducing disruption to business operations.
- Enhanced Equipment Longevity: Proper setup protects equipment from damage and ensures peak performance over time.
- Improved User Experience: Customers benefit from intuitive setups and clear guidance, allowing them to use their equipment confidently.
- Cost Savings: Avoiding installation errors reduces the likelihood of costly repairs or replacements down the line.
Field service installations are not merely about placing and powering up equipment—they are about delivering a robust foundation for success. By leveraging skilled technicians and proven methodologies, businesses can ensure a smooth transition from purchase to performance.
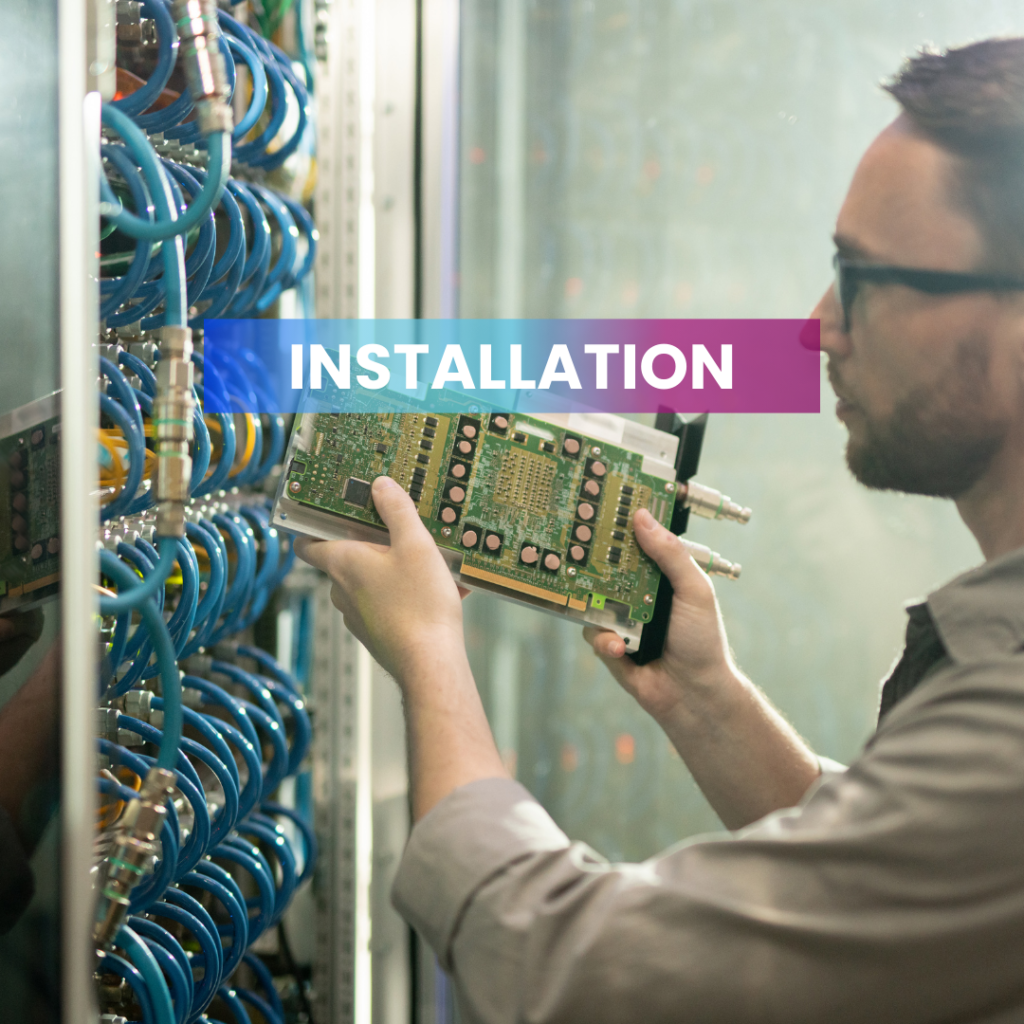
Key Steps in Field Service Installation
Site Assessment and Preparation
Before installation begins, field technicians conduct a thorough site assessment to evaluate the physical space, environmental conditions, and infrastructure compatibility. This ensures that the equipment can be installed safely and will perform effectively. Key activities include:- Verifying power supply and connectivity requirements.
- Identifying any structural modifications needed.
- Addressing potential environmental challenges, such as temperature control or interference.
Logistics and Coordination
Effective installation starts with meticulous planning and coordination. This includes:- Scheduling installation times that minimize disruption to the customer’s operations.
- Ensuring all necessary equipment, tools, and components are available on-site.
- Coordinating with other contractors or teams involved in the setup.
Equipment Setup and Configuration
During the installation process, technicians carefully unpack, assemble, and position the equipment as per the design plan. This step involves:- Mounting and securing devices, such as CCTV cameras, network switches, or industrial machinery.
- Calibrating equipment to ensure precision and accuracy.
- Configuring software and hardware settings to meet the customer’s specific requirements.
System Integration
For many businesses, new equipment needs to integrate seamlessly with existing systems. Field service technicians ensure:- Compatibility with current networks, software, or workflows.
- Smooth data migration, if necessary.
- Proper synchronization between old and new systems to avoid operational hiccups.
Testing and Validation
Once the equipment is installed, rigorous testing ensures that everything is functioning as expected. Technicians:- Conduct performance tests to verify system efficiency and reliability.
- Simulate real-world conditions to check for potential issues.
- Fine-tune settings for optimal performance.
Customer Training and Handover
A successful installation goes beyond setup—it involves empowering the customer to use the equipment effectively. This includes:- Providing a detailed walkthrough of the system’s features and functionality.
- Offering hands-on training sessions for key personnel.
- Supplying user manuals and support documentation for future reference.
Post-Installation Support
After the installation is complete, ongoing support ensures customer satisfaction. Field service teams:- Monitor system performance remotely, if applicable.
- Schedule follow-up visits to address any concerns or adjustments.
- Offer maintenance recommendations to prevent future issues.