What is Field Services?
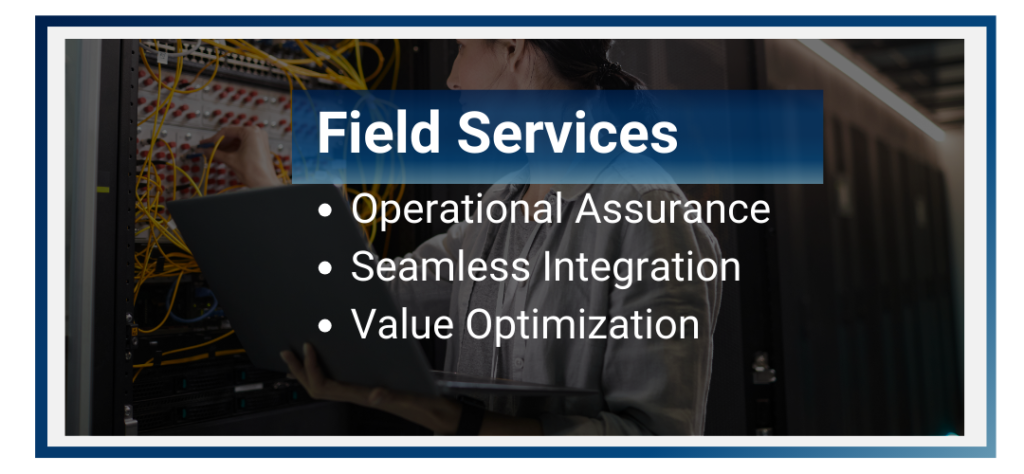
Field services are fundamentally a people-oriented business consisting of field technicians, also known as field service engineers or field forces, who perform services for your customers at their location. Optimized field operation coordinates all operations conducted by a field service organization, such as scheduling service, dispatching technicians, tracking job status, invoicing, and billing. For 20+ years, DRI Systems has been the trusted choice for optimizing field services across various industries, ensuring your operations are seamless and cost-effective.
Field Services with DRI Systems
Our team of experienced technicians and engineers are ready to facilitate the most important on-site factor in the IT service equation: Field Services. We provide:
- Complex technology refreshes
- Network equipment rack-and-stack
- Device deployment
- Structured cabling services
- Site assessments
- Equipment moves and migrations
Why Field Services Matter
Field services are the backbone of many industries, ensuring the proper installation, maintenance, and repair of critical systems and equipment at customer locations. This is pivotal for industries like:
- Enterprise IT
- Healthcare Technology
- Industrial Equipment
With DRI Systems, you can rest assured that your field services are aligned with industry best practices, improving outcomes while reducing costs.
Different Types of Field Service Activities
Here are the main categories of field services that can be delivered:
Installation in Field Service
Installation is the foundation of effective field service operations. It sets the stage for the long-term functionality and performance of equipment, ensuring that customers experience optimal results from day one. In the context of field services, installation encompasses a range of critical steps designed to seamlessly integrate new equipment into a customer’s operating environment while adhering to industry best practices and specific client requirements.
Benefits of Professional Field Service Installation
- Minimized Downtime: Expert installation ensures quick deployment, reducing disruption to business operations.
- Enhanced Equipment Longevity: Proper setup protects equipment from damage and ensures peak performance over time.
- Improved User Experience: Customers benefit from intuitive setups and clear guidance.
- Cost Savings: Avoiding installation errors reduces the likelihood of costly repairs.
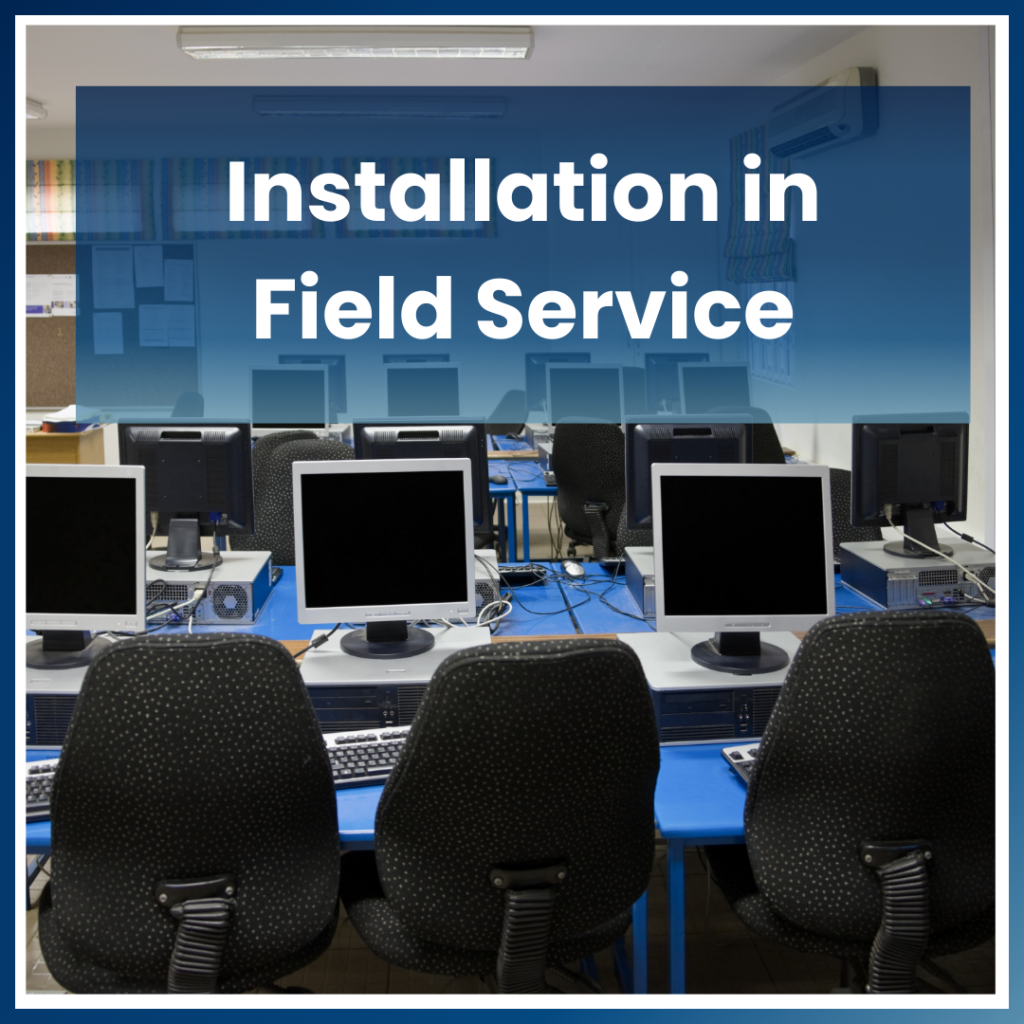
Key Steps in Field Service Installation
1. Site Assessment and Preparation
Before installation begins, field technicians conduct a thorough site assessment to evaluate the physical space, environmental conditions, and infrastructure compatibility. This ensures that the equipment can be installed safely and will perform effectively. Key activities include:
- Verifying power supply and connectivity requirements.
- Identifying any structural modifications needed.
- Addressing potential environmental challenges, such as temperature control or interference.
2. Logistics and Coordination
Effective installation starts with meticulous planning and coordination. This includes:
- Scheduling installation times that minimize disruption to the customer’s operations.
- Ensuring all necessary equipment, tools, and components are available on-site.
- Coordinating with other contractors or teams involved in the setup.
3. Equipment Setup and Configuration
During the installation process, technicians carefully unpack, assemble, and position the equipment as per the design plan. This step involves:
- Mounting and securing devices, such as CCTV cameras, network switches, or industrial machinery.
- Calibrating equipment to ensure precision and accuracy.
- Configuring software and hardware settings to meet the customer’s specific requirements.
4. System Integration
For many businesses, new equipment needs to integrate seamlessly with existing systems. Field service technicians ensure:
- Compatibility with current networks, software, or workflows.
- Smooth data migration, if necessary.
- Proper synchronization between old and new systems to avoid operational hiccups.
5. Testing and Validation
Once the equipment is installed, rigorous testing ensures that everything is functioning as expected. Technicians:
- Conduct performance tests to verify system efficiency and reliability.
- Simulate real-world conditions to check for potential issues.
- Fine-tune settings for optimal performance.
6. Customer Training and Handover
A successful installation goes beyond setup—it involves empowering the customer to use the equipment effectively. This includes:
- Providing a detailed walkthrough of the system’s features and functionality.
- Offering hands-on training sessions for key personnel.
- Supplying user manuals and support documentation for future reference.
7. Post-Installation Support
After the installation is complete, ongoing support ensures customer satisfaction. Field service teams:
- Monitor system performance remotely, if applicable.
- Schedule follow-up visits to address any concerns or adjustments.
- Offer maintenance recommendations to prevent future issues.
Maintenance in Field Service
Maintenance is a cornerstone of field service operations, ensuring that equipment functions optimally and downtime is minimized. Traditionally, field service organizations were reactive, focusing on fixing equipment after it broke down. However, modern practices emphasize a proactive and predictive approach, which not only improves customer satisfaction but also reduces operational costs. Let’s explore the various types of maintenance activities in field services and their benefits.
Why Maintenance Matters in Field Services
- Cost Savings: Proactive and preventive maintenance reduce the likelihood of costly emergency repairs and production losses.
- Increased Equipment Lifespan: Regular upkeep ensures machines operate efficiently for longer periods.
- Enhanced Safety: Properly maintained equipment reduces the risk of accidents or malfunctions.
- Improved Customer Trust: Reliable equipment performance builds customer confidence and loyalty.
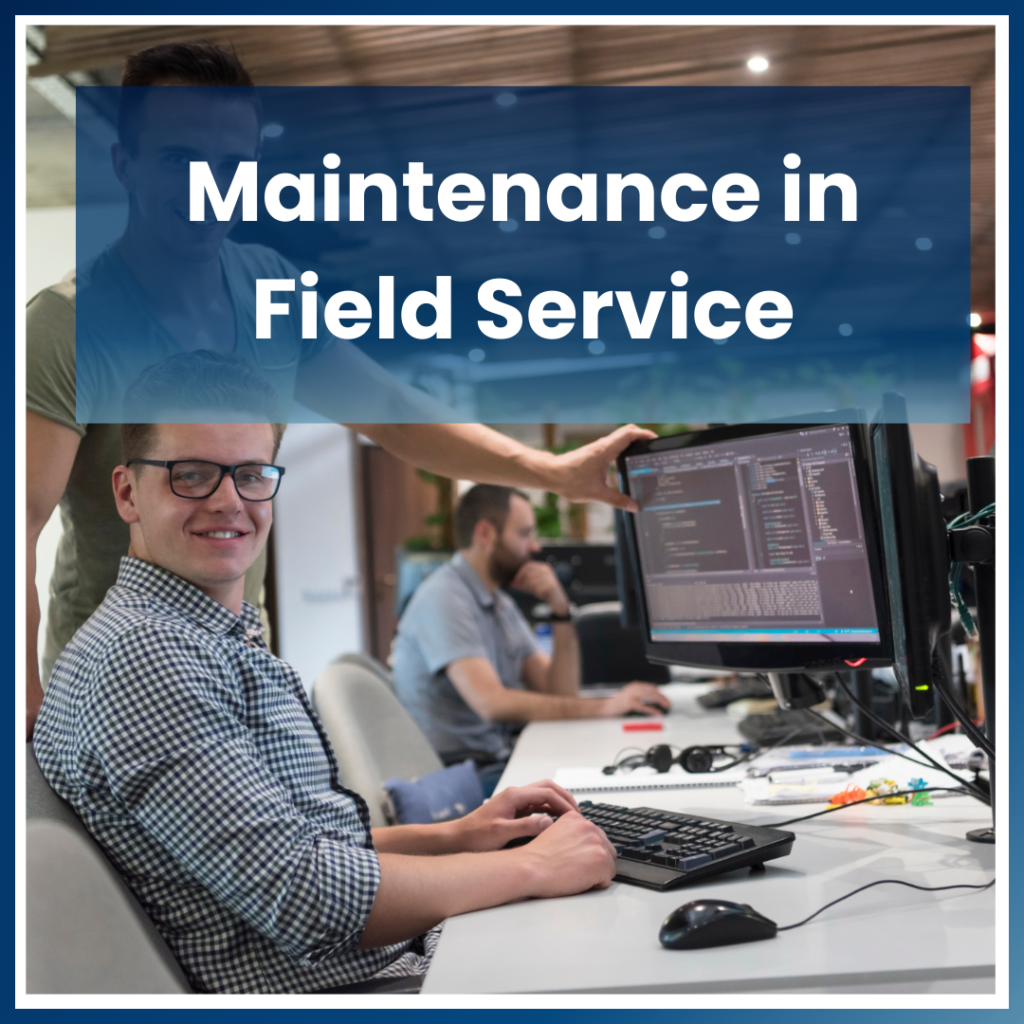
1. Corrective Maintenance
Corrective maintenance involves addressing issues after they occur, typically triggered by a malfunction or performance irregularity.
Key Activities in Corrective Maintenance:
- Repairs: Fixing damaged or non-operational equipment to restore functionality.
- Calibration: Ensuring machinery is functioning according to specifications, particularly for precision-dependent equipment like sensors or medical devices.
Advantages:
- Direct response to existing issues.
- Allows for immediate problem resolution, reducing prolonged downtime.
Challenges:
- Can be costly if the breakdown leads to production delays.
- Unplanned repairs may disrupt business operations.
2. Preventive Maintenance
Preventive maintenance focuses on regular, planned activities to inspect and maintain equipment before issues arise.
Key Activities in Preventive Maintenance:
- Routine Inspections: Checking equipment for wear and tear or potential issues.
- Parts Replacement: Proactively replacing components like filters, belts, or gaskets that show signs of wear.
- Lubrication and Cleaning: Ensuring machinery runs smoothly and without blockages.
Technological Enhancements:
- Connected Devices: Using IoT-enabled devices to collect and analyze performance data, providing insights into equipment health.
- Performance Monitoring: Observing real-time data to detect any deviations from normal operation.
Advantages:
- Significantly reduces the likelihood of breakdowns.
- Enhances equipment lifespan and reliability.
- Minimizes unexpected downtime, keeping operations smooth.
3. Proactive Maintenance
Proactive maintenance takes preventive strategies a step further by using advanced tools and analytics to predict potential failures before they occur.
Key Activities in Proactive Maintenance:
- Predictive Analytics: Analyzing historical and real-time data to identify patterns that may indicate future issues.
- Condition-Based Monitoring: Using sensors to continuously assess equipment conditions, such as vibration levels, temperature, and pressure.
- Fault Prediction: Employing machine learning algorithms to compare current operations with optimal benchmarks and flag anomalies.
Advantages:
- Nearly eliminates unexpected breakdowns.
- Reduces the cost of emergency repairs and service disruptions.
- Optimizes the use of spare parts and technician time.
Technological Tools:
- Digital Twins: Virtual models of physical assets used to simulate and predict maintenance needs.
- AI-Powered Systems: Automated tools that identify trends and recommend actionable insights.
Adoption Services
Adoption services are the bridge between technical excellence and exceptional customer experiences. By advising customers on how to make the most of their equipment, field service technicians play a pivotal role in building trust and loyalty. Investing in this proactive and consultative approach not only solves immediate challenges but also paves the way for long-term growth and success for both the customer and your business.
In addition to in-person repair and maintenance visits, field technicians can advise customers on maximizing the benefits of equipment based on their desired outcomes.
Field service technicians are uniquely positioned to become a customer’s trusted advisor. They take on a proactive and consultative role in helping customers get the most out of their purchases, whether it’s through optimizing operations, or even adding additional products and services to their contracts. You can be confident in your team’s ability to provide valuable advice and support to your customers, knowing they are fixing problems.
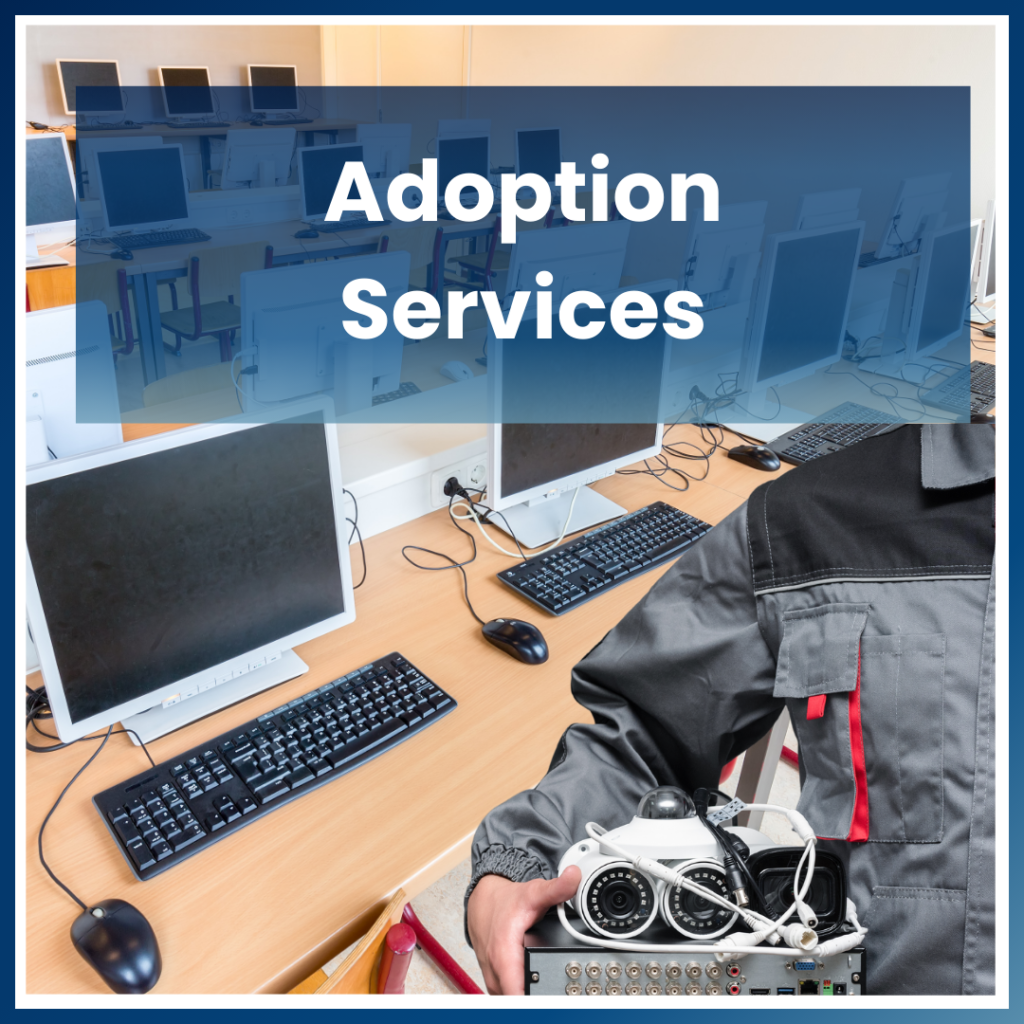
1. Enhancing Equipment Utilization
Field technicians are uniquely qualified to help customers maximize the potential of their equipment, ensuring it performs effectively and aligns with their operational goals.
Key Activities in Adoption Services:
- Usage Optimization: Advising customers on how to configure and use equipment for peak efficiency.
- Training and Demonstrations: Providing hands-on training sessions to familiarize customers with advanced features.
- Customization: Recommending adjustments or enhancements that suit the specific needs of the customer.
Customer Benefits:
- Improved productivity and workflow.
- Extended equipment lifespan through proper use.
- Greater confidence in the technology they have invested in.
2. Consultative Role of Field Technicians
By adopting a proactive mindset, field technicians can become invaluable advisors who contribute to the customer’s long-term success.
Key Responsibilities:
- Outcome-Focused Recommendations: Offering tailored advice based on the customer’s desired outcomes. For instance, a manufacturing client might need tips on reducing downtime, while a retail client might benefit from streamlined point-of-sale operations.
- Proposing Additional Solutions: Identifying opportunities to enhance performance through complementary products or upgrades.
- Feedback Loops: Gathering insights from the customer’s real-world usage to refine processes and suggest improvements.
Business Benefits:
- Positions your organization as a comprehensive service provider.
- Strengthens customer loyalty and trust.
- Opens doors to upselling and cross-selling opportunities.
3. Adding Value Through Technology and Expertise
Modern field services rely on a blend of technical know-how and cutting-edge tools to deliver value-driven adoption services.
Key Tools for Enhanced Customer Guidance:
- IoT and Data Insights: Leveraging data from connected devices to provide performance-based recommendations.
- Mobile Apps for Support: Technicians can share user manuals, video tutorials, or step-by-step guides during in-person visits.
- Augmented Reality (AR): Offering real-time, visual demonstrations for operating or troubleshooting equipment.
Examples of Added Value:
- Identifying underutilized features that could improve efficiency.
- Advising on software updates or system integrations that enhance functionality.
- Ensuring safety compliance through best-practice recommendations.
4. Managerial Confidence in Adoption Services
Field service managers can trust their teams to go beyond technical fixes and focus on creating meaningful customer experiences.
Empowering Field Teams:
- Comprehensive Training: Equip technicians with both technical and interpersonal skills to serve as knowledgeable consultants.
- Knowledge-Sharing Systems: Provide access to a centralized database of best practices, manuals, and case studies.
- Customer-Centric Culture: Encourage technicians to view every service interaction as an opportunity to educate and empower the customer.
5. Long-Term Impact of Adoption Services
Integrating adoption services into your field service strategy has far-reaching benefits:
For Customers:
- Enhanced ROI from their investment.
- Reduced downtime and frustration through optimized usage.
- Confidence in working with a proactive and knowledgeable service partner.
For Your Business:
- Increased customer retention through higher satisfaction levels.
- New revenue streams from upgrades and additional services.
- Differentiation in a competitive market by offering value-added services.